Hardness is a measure of a material’s ability to resist abrasion and indentation. For carbon steels Brinell & Rockwell hardness testing can be used to estimate tensile strength. | |
Toughness is a material’s ability to absord impact or shock loading, and is rarely a specification requirement. | |
Ductility is the measurement of a material to deform before it fails and fractures. | |
Elongation is the extension of a material in a tension test at any point and is probably the characteristic that renders the most complications in fasteners. A material that exhibits little or no plastic deformity at its fracture point is considered brittle. |
Tensile Strength
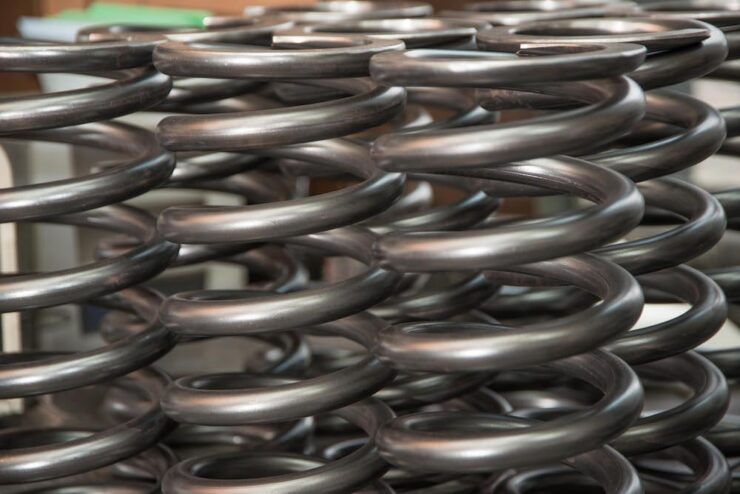
It is the ultimate strength of a given alloy or product that determines how much load it can withstand before breaking, or being pulled apart. It is calculated by performing a tension test and determining at what tensile strength maximum load is reached. i.e. how much force is needed in psi, pounds per square inch, to break it. Tensile strength figures in PSI are used as a common standard in comparing different metals.
Proof Load
It is applied tensile load that fastener must support without permanent deformation and represents the usable strength of a certain standards.
Thread Strength
It should be taken into consideration as the threaded section is the weakest part of the fastener so it remains a critical aspect of strength and clamping force. The proper assembly should always have fasteners of equal grade working to meet their ultimate tensile strength.
This diagram shows the strain on a fastener being stretched to the point of failure (fracture). The initial slope shows how the stress being applied to the fastener is straining and stretching it. Here the fastener is still in the elastic range, and will return to its normal shape once the stress in removed. At the yield point the fastener gives and begins to elongate throughout the plastic range, where it will no longer return to its shape prior to being stretched if the load is removed. As the fastener passes its ultimate tensile strength it will no longer be able to carry an applied load, and will eventually fail at its fracture point.
Creep
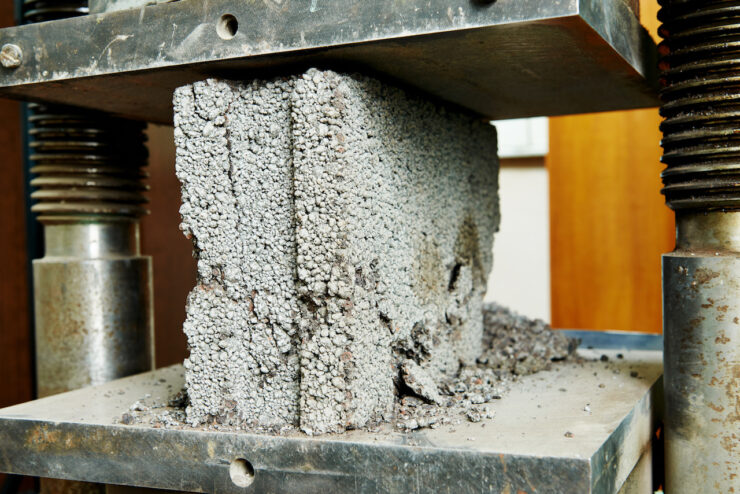
At ordinary temperatures metals under load normally change their dimensions only when the load they are under is changed. At elevated temperatures, however, dimensional changes take place even under constant load. Metals, and other materials creep. For example, a bolt under a constant tensile load at high temperatures will elongate continuously. The higher the temperature the fastener will elongate, i.e., the higher the creep rate.
Fatigue Strength
It is subjected to repeated cyclic loads can suddenly and unexpectedly break, even if the loads are well beneath the strength of the material. Fatigue strength is the maximum stress it can withstand for a specified number of repeated load cycles prior to its failure.
Shear Strength
Shear Strength is the maximum load that can be supported prior to fracture when applied at a right angle to the fastener’s axis. It is opposite from tensile strength in that tensile strength is a measured longitudinal pull, while shear strength is caused by a push or pull 90’ from the longitudinal axis. A single shear joint occurs when there is a load occurring in one transverse plane and if the shear strength was exceeded the fastener would be broken into two pieces. Double shear is a load applied in two planes where the fastener could be broken into three pieces.
Torque
It is a twisting force that causes the rotation of a shaft or will set up a twist in a stationary shaft and is generally expressed in foot-pounds (ft-lbs) or inch-pounds. Properly threaded products achieve their clamping load from the tension or torque that is derived from the mating of the external and internal threads.
Torsional Strength is a load usually expressed in terms of torque, at which the fastener fails by being twisted off its axis. Tapping screws and sockets set screws require a torsional test.
Strength-to-Weight-Ratio
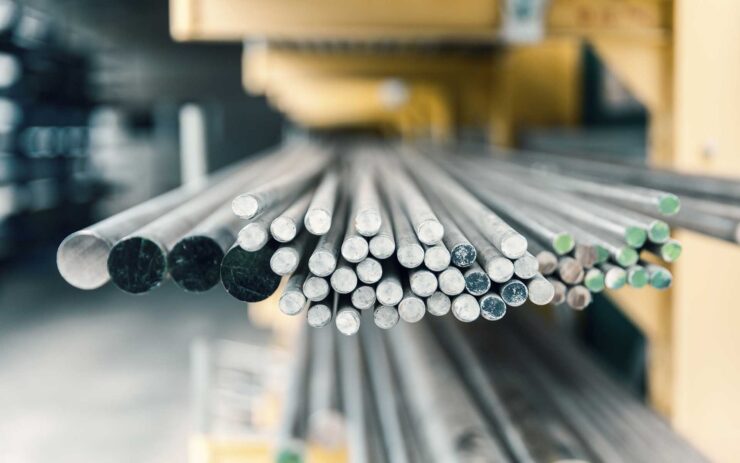
In application where load supporting parts are to be lifted or moved against the pull of gravity the strength-to-weight ratio (SWR) becomes an important figure. SWR is defined as the ratio of the tensile strength to the density of the material, the density being the weight per unit volume.
Temperature Effects: Elevated and Cryogenic
Each come with a set of static and dynamic strengths that are determined by their manufacturing process, composition, and size. In application, a range of factors including temperature variation affects the availability of these strengths. Every bolting material has a temperature above which it would be unsafe to use; this is often times referred to as the high temperature service limit.
Although a fastener loses strength as the temperature increases, the service limit is usually determined by an occurrence known as stress relaxation.
A fastener is bolted into a joint, which places it under significant stress. When the temperature rises the bolts begins to relieve itself of a significant amount of stress. Science stress and preload are related, the clamping force that the bolt is exerting to hold the joint together will be greatly reduced.
At very cold temperatures these same molecular bonds lose their ability to expand and flex, which is needed to relieve fastening stress under application load. As a result, it can become brittle at low temperature and also provides less than room temperature fastening performance.