Almost 90% of all fasteners are made of carbon steel. A plain carbon steel is one in which carbon is the only alloying element added to the iron base. The amount of carbon in the steel controls its hardness, strength, and ductility.
Low Carbon Steel
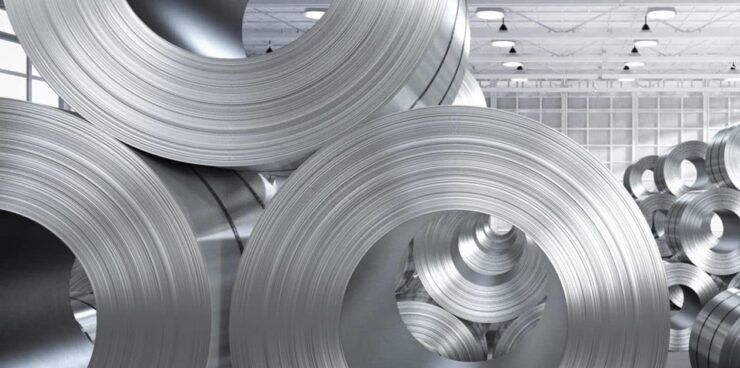
Low carbon steel generally contains less than 0.25% carbon and cannot be strengthened by heat-treating; strengthening may only be accomplished through cold working and case hardening. The low carbon material is relatively soft and week, but has outstanding ductility and toughness; in addition, it is machinable, weldable and is relatively inexpensive to produce. The most commonly used chemical analyses include AISI 1006, 1008, 1016, 1018, 1021, and 1022.
Medium Carbon Steel
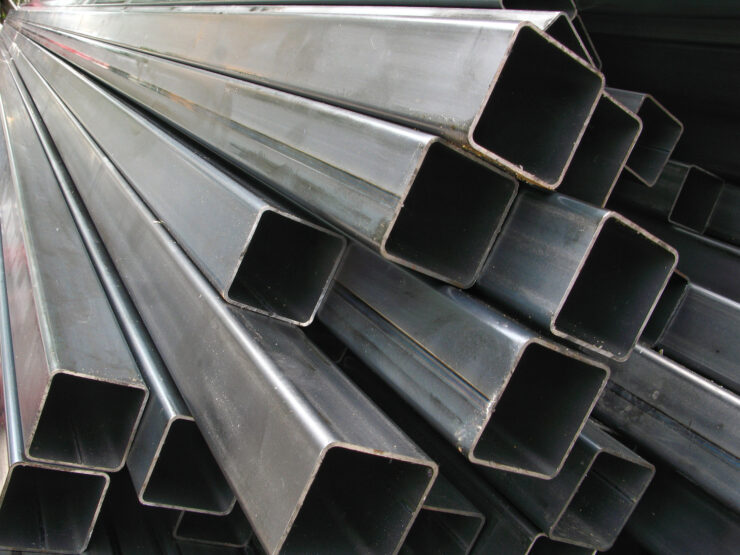
Medium carbon steel have carbon concentrations between about 0.25% and 0.60%. these steels may be heat treated by austenizing, quenching and then tempering to improve their mechanical properties. The plain medium carbon steels have low hardenabilities and can be successfully heat treated only in thin sections and with rapid quenching rates. Notices on the SAE J429, ASTM A325, and ASTM A449 specifications that their strength properties “step down” as the diameters increase. The popular chemical analyses include AISI 1030, 1035, 1038, and 1541 Alloy Steel.
High and Very High Carbon Steel
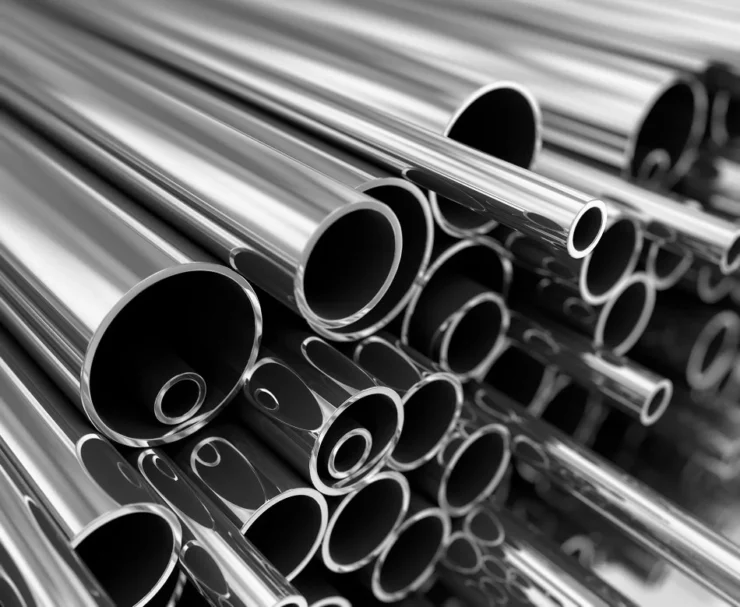
Steels with a carbon range of 0.45% to0.75% are classified as high-carbon and those with 0.75% to 1.7% carbon as very-high-carbon steels. Both of these steels respond well to heat treatment. As a rule, steels up to 0.65% carbon can be welded with special electrodes, although preheating and stress relieving techniques must often be used after the welding is completed. This form of steel has the best hardness, strength and ductility. The areas best suited for this steel are in tools, drills, saws, knife blades, and bearing. High carbon content reduces the wear and deformation of the steel.
Alloy Steel
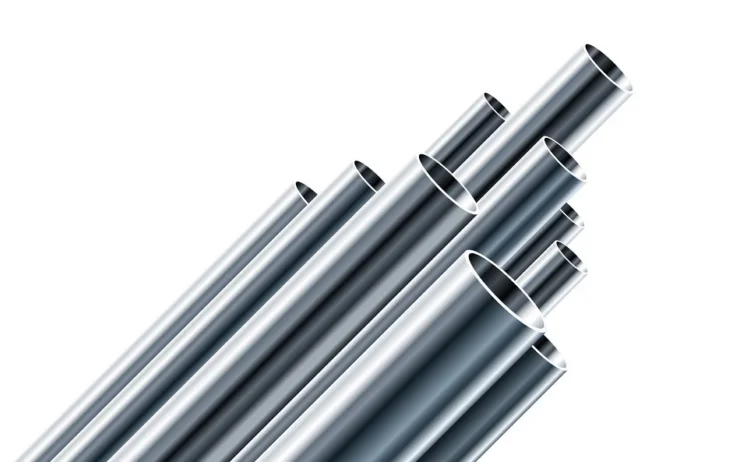
Carbon steel is classed as an alloy steel when it contains more than 1.65% manganses, 0.60% silicon, or 0.60% copper, or when chromium content is less than 4%. Dozens of different carbon alloy steels are used for fasteners: AISI 1335(Mg), 4037(Mo), 4140(Cr, Mo) M 4340(Ni,Cr, Mo), 8637(Ni, Cr, Mo), and 8740(Ni, Cr, Mo), for examples.
![]() |
Manganese (Mn) contributes strength, moderately improves hardenability, and is beneficial to surface quality. |
![]() |
Nickel (Ni) provides strength, improves toughness at low temperature, benefits corrosion resistance, and adds to the heat treat process, which assure more consistent results. |
![]() |
Chromium(Cr) increases hardenability, reduces susceptibility to temper brittleness, and has a powerful positive effect on temperature, tensile and creep strengths. |
![]() |
Sulphur(S) increases machinability, but causes lower strength at elevated temperatures. |
Stainless Steel
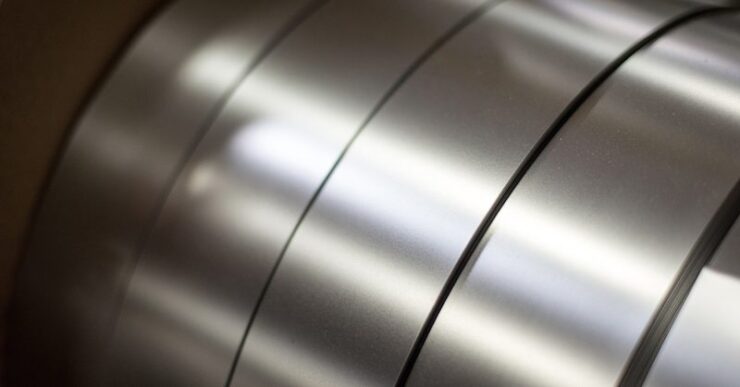
Stainless steel is a family of iron-based alloys that must contain at least 10.5% chromium. The presence of chromium creates an invisible surface film that resists oxidation and makes the materials “passive” or corrosion resistance. Other elements, such as nickel or molybdenum are added to increase corrosion resistance, strength or heat resistance. Stainless steels can be simply and logically divided into three classes on the basis of their microstructure; martensitic, ferritic or austenitic. Each of these classes has specific properties and basic grade or “type”.
![]() |
Austenitic : 18-8 ( the commercial grade) or 300 series (303 & 304 are common). This chromium-nickel type contains about 18% chromium and 8% nickel, is not hardenable by heat treatment, non magnetic ( in it’s annealed condition-it will become more so due to cold-working), and offers the greatest degree of corrosion resistance. 316 has a higher nickel content and offers higher corrosion resistance in certain chemical and seawater environments. About 80% of all stainless steel fasteners are produced from this type of steel. |
![]() |
Martensitic : Contains from 12-20% chromium, is magnetic, and because they are heat-treated they are high-strength. Type 410 and 416 are of this group and common fastening alloys. Suitable for industrial and medical applications, 400 series martensitic steel is much more corrosion-resistant than carbon steel and can be sharpened to equally-keen edge sharpness. |
![]() |
Ferritic : These are also chromium stainless alloys that can be case hardened. Type 430 falls into this class. This type of stainless steel is magnetic, non-hardenable by heat treatment and has very poor weld characteristics. They should not be used in situations of high corrosion resistance requirements, such as marine use or on building exteriors .The most common places to use Stainless Steel are in areas of corrosion and tempering, or were strength is required. Because of its corrosion resistant qualities and ability to attain a mirror-like finish, it is one of the most versatile of all metals. |
![]() |
Sulphur(S) increases machinability, but causes lower strength at elevated temperatures. |